How to choose the right PCB material for your application
Quendler
Posted on July 12, 2023
Selecting the right PCB material is a critical decision in the design and manufacturing process. The choice of material impacts the overall performance, reliability, and cost of the printed circuit board (PCB). In this article, we will explore the factors to consider when choosing a PCB material for your specific application. By understanding the characteristics and trade-offs of different materials, you can make an informed decision that aligns with your project requirements.
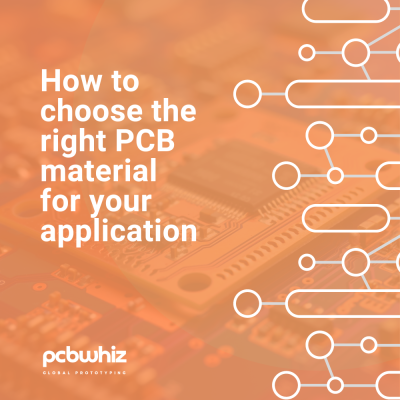
1. Understanding PCB Material Properties:
Before diving into the selection process, it's essential to have a basic understanding of the key properties of PCB materials:
- Dielectric constant (Dk): Determines the material's ability to store electrical energy and affects signal propagation speed.
- Dissipation factor (Df): Indicates the material's ability to dissipate electrical energy as heat and impacts signal integrity.
- Thermal conductivity: Affects the board's ability to dissipate heat and influences its thermal management capabilities.
- Moisture absorption: The extent to which a material absorbs moisture, which can impact its electrical performance and reliability.
- Flame resistance: Indicates the material's resistance to fire and its compliance with safety standards.
- Mechanical properties: Considerations such as rigidity, flexibility, and impact resistance that affect the board's durability.
2. Identifying Application Requirements:
To choose the right PCB material, you need to assess the specific requirements of your application. Consider the following factors:
- Operating environment: Will the PCB be exposed to extreme temperatures, humidity, or chemicals? Select a material that can withstand the environmental conditions.
- Frequency and speed: If your design involves high-frequency signals or fast data transmission, opt for a material with low Dk and Df values for better signal integrity.
- Power dissipation: If your application generates significant heat, choose a material with high thermal conductivity to efficiently dissipate heat.
- Size and weight constraints: If space is limited or weight is a concern, consider materials that offer high density and lightweight properties.
- Manufacturing processes: Some materials may require specific manufacturing techniques or have restrictions, so evaluate compatibility with your chosen fabrication processes.
3. Common PCB Materials:
There are several commonly used PCB materials, each with its own characteristics and suitability for different applications. Here are a few examples:
- FR-4: The most widely used material due to its cost-effectiveness, electrical insulation properties, and good overall performance. And high-Tg FR-4 offers higher glass transition temperature (Tg) than standard FR-4, making it suitable for applications with elevated temperature requirements.
- Metal core (MCPCB): Features a metal core for efficient heat dissipation, making it suitable for power electronics and LED applications.
- Polyimide (PI): Exhibits excellent flexibility, high-temperature resistance, and low moisture absorption, making it suitable for flexible PCBs and aerospace applications.
- Rogers: Known for its high-frequency performance, low loss, and stable dielectric properties, making it ideal for RF and microwave applications.
4. Considering Trade-Offs and Cost:
While evaluating different PCB materials, it's crucial to consider the trade-offs associated with each option. Higher-performing materials often come at a higher cost, so it's essential to find a balance between performance and budget. Assess the specific needs of your application and weigh factors such as electrical performance, thermal management, and reliability against the associated costs.
5. Seeking Expert Advice:
Choosing the right PCB material can be complex, especially for specialized applications or unique requirements. Don't hesitate to consult with PCB manufacturers, material suppliers, or experienced design engineers. They can provide valuable insights and recommendations based on their expertise and knowledge of industry trends.
Selecting the right PCB material is a crucial step in the design and manufacturing process. By understanding the properties and characteristics of various materials, engineers can make informed decisions based on the specific requirements of their applications.
FR-4 remains the most widely used and versatile material due to its excellent electrical performance, mechanical strength, and thermal stability. It is suitable for a wide range of applications, including consumer electronics, telecommunications, and industrial equipment.
However, in cases where cost is a primary consideration and the application does not demand high-performance features, materials like CEM-1 and CEM-3 can be viable options. These composite materials offer satisfactory electrical insulation and mechanical strength at a lower price point.
When choosing a PCB material, it's essential to consider factors such as operating environment, signal integrity requirements, thermal management, and manufacturing processes. Collaborating with experienced PCB manufacturers and suppliers can provide valuable insights and assistance in material selection.
Ultimately, the right PCB material choice is about striking the right balance between performance, cost, and the specific needs of the application. By evaluating the benefits and drawbacks of different materials and considering the project's requirements, engineers can ensure the successful development of reliable and high-performing electronic devices.
Remember, the PCB material is the foundation upon which the entire electronic system is built. So, take the time to research and select the material that best aligns with your design goals and application requirements. Making an informed decision at this early stage can save time, cost, and potential performance issues in the long run.
Keep Reading...
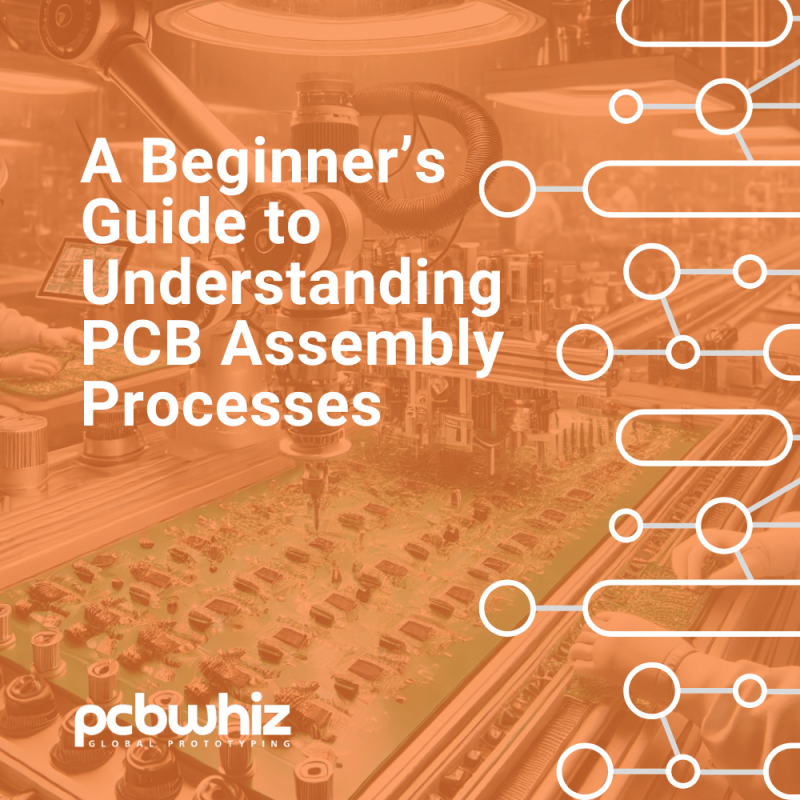
A Beginner’s Guide to Understanding PCB Assembly Processes
Die Leiterplattenbestückung (Printed Circuit Board Assembly, PCBA) ist eine entscheidende
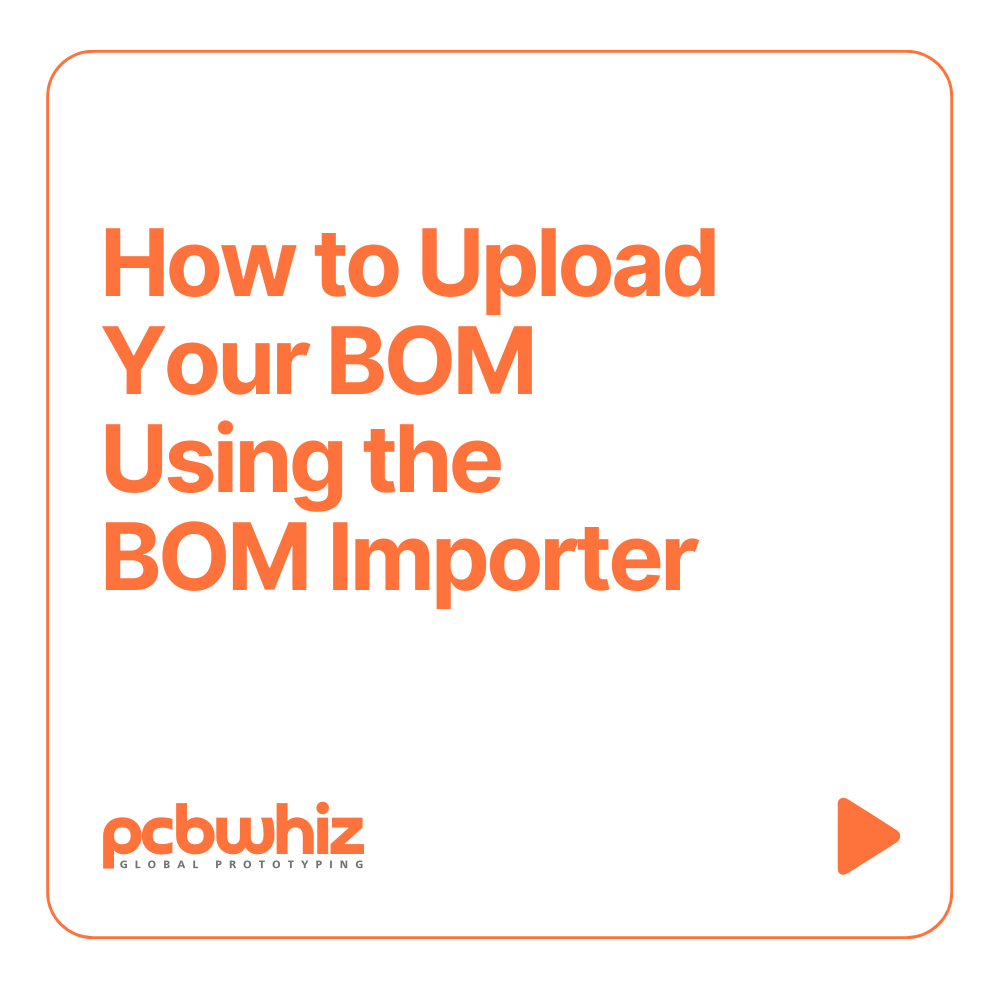
How to Upload Your BOM Using the BOM Importer
Richtlinien für das Format Ihrer Stückliste (BOM) Unterstützte Dateiformate Sie
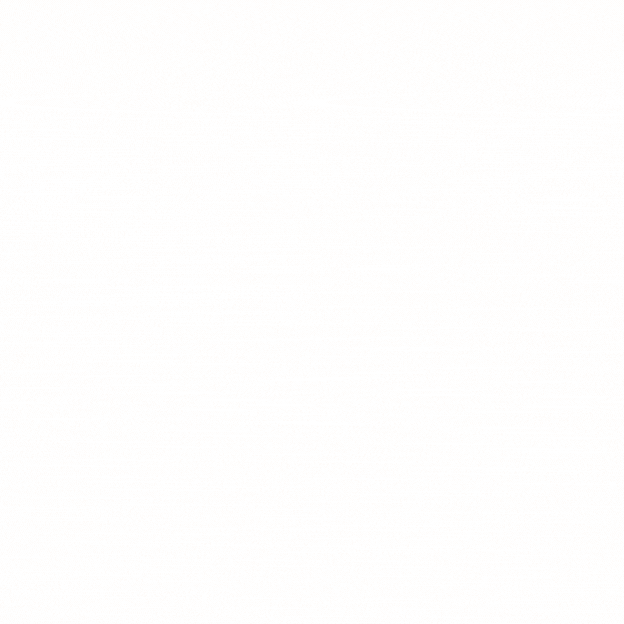
Happy new year 2024!
Während wir das Jahr 2024 begrüßen, denken wir an die