Introduction to PCB Surface Finishes: Why Are They Important?
Martin Huang
Posted on February 4, 2025
Printed Circuit Boards (PCBs) are the backbone of modern electronics, providing mechanical support and electrical connections for components. However, copper traces on an unprotected PCB oxidize upon exposure to air, compromising solderability and long-term reliability. To prevent this, a surface finish is applied to the exposed copper areas, ensuring optimal performance during assembly and throughout the product’s lifecycle. In this article, we explore the role of PCB surface finishes, key selection factors, and an overview of the most common types.
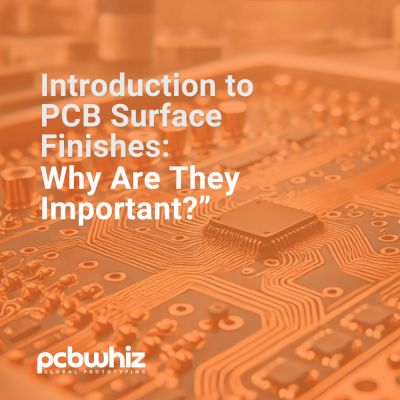
What is a PCB Surface Finish?
A PCB surface finish is a protective coating applied to exposed copper to maintain solderability, prevent oxidation, and enhance electrical performance. It plays a crucial role in component assembly by ensuring that solder joints are strong and reliable.
Different applications require different surface finishes, depending on factors such as assembly method, environmental conditions, and cost. The right choice can extend a PCB’s lifespan, reduce defects, and ensure compliance with industry standards.
Why Are Surface Finishes Important?
1. Prevention of Oxidation – Copper oxidizes quickly, leading to poor solderability. Surface finishes provide a barrier against oxidation and contaminants.
2. Solderability – The finish affects how well solder adheres to the PCB during assembly, impacting joint strength and reliability.
3. Electrical Performance – Some finishes offer better conductivity and lower contact resistance, which is crucial for high-frequency applications.
4. Durability and Shelf Life – The type of finish influences how long a PCB can be stored before assembly without degradation.
5. RoHS Compliance – Many industries now require RoHS-compliant (lead-free) surface finishes for environmental and regulatory reasons.
Common Types of PCB Surface Finishes
Various PCB surface finishes are available, each with advantages and disadvantages depending on application, production volume, and cost. Here is an overview of the most widely used options:
1. Hot Air Solder Leveling (HASL & Lead-Free HASL)
• Description: A thin solder layer (typically tin-lead or lead-free) is applied and leveled with hot air knives.
• Advantages: Cost-effective, widely used, good solderability.
• Disadvantages: Uneven surface can affect fine-pitch components, not ideal for HDI boards.
• Best suited for: Standard PCBs, simple to moderately complex designs.
2. Electroless Nickel Immersion Gold (ENIG)
• Description: A nickel layer protects the copper, topped with a thin immersion gold layer.
• Advantages: Smooth surface, excellent oxidation resistance, long shelf life.
• Disadvantages: More expensive than HASL, potential risk of "Black Pad" defects.
• Best suited for: High-reliability applications, fine-pitch components, RoHS-compliant designs.
3. Organic Solderability Preservative (OSP)
• Description: A water-based organic compound forms a thin protective layer over the copper.
• Advantages: Lead-free, cost-effective, simple process.
• Disadvantages: Short shelf life, sensitive to handling, not suitable for multiple reflow cycles.
• Best suited for: High-volume consumer electronics, cost-sensitive applications.
4. Immersion Silver
• Description: A thin silver layer is chemically applied to the copper surface.
• Advantages: Smooth surface, good conductivity, RoHS compliant.
• Disadvantages: Prone to tarnishing, requires careful storage and handling.
• Best suited for: High-frequency applications, RF and microwave PCBs.
5. Immersion Tin
• Description: A tin layer is chemically deposited onto the copper.
• Advantages: Smooth surface, good for fine-pitch components, RoHS compliant.
• Disadvantages: Short shelf life, risk of tin whiskers.
• Best suited for: Automotive and backplane PCBs.
6. Electroless Nickel Electroless Palladium Immersion Gold (ENEPIG)
• Description: Similar to ENIG but with an additional palladium layer between nickel and gold.
• Advantages: Excellent oxidation resistance, prevents "Black Pad" issues.
• Disadvantages: Expensive, complex process.
• Best suited for: High-reliability applications, wire bonding.
How to Choose the Right Surface Finish?
Selecting the best PCB surface finish depends on several factors:
• Assembly Method: SMT, THT, or hybrid assembly may require different finishes.
• Component Type: Fine-pitch components need a smooth, even surface.
• Environmental Conditions: Harsh environments require oxidation-resistant finishes like ENIG or ENEPIG.
• Production Volume: High-volume PCBs often favor cost-effective solutions like HASL or OSP.
• Shelf Life: If long storage is required, ENIG or immersion silver may be beneficial.
Final Thoughts
PCB surface finishes play a critical role in reliability, performance, and manufacturability. Choosing the right one requires careful consideration of cost, performance, and application requirements. In the next part of this series, we will take a deeper dive into the advantages and limitations of specific finishes to help you make an informed decision for your PCB projects.
Stay tuned for Part 2: HASL vs. ENIG – A Detailed Comparison of the Most Common PCB Surface Finishes!
Keep Reading...
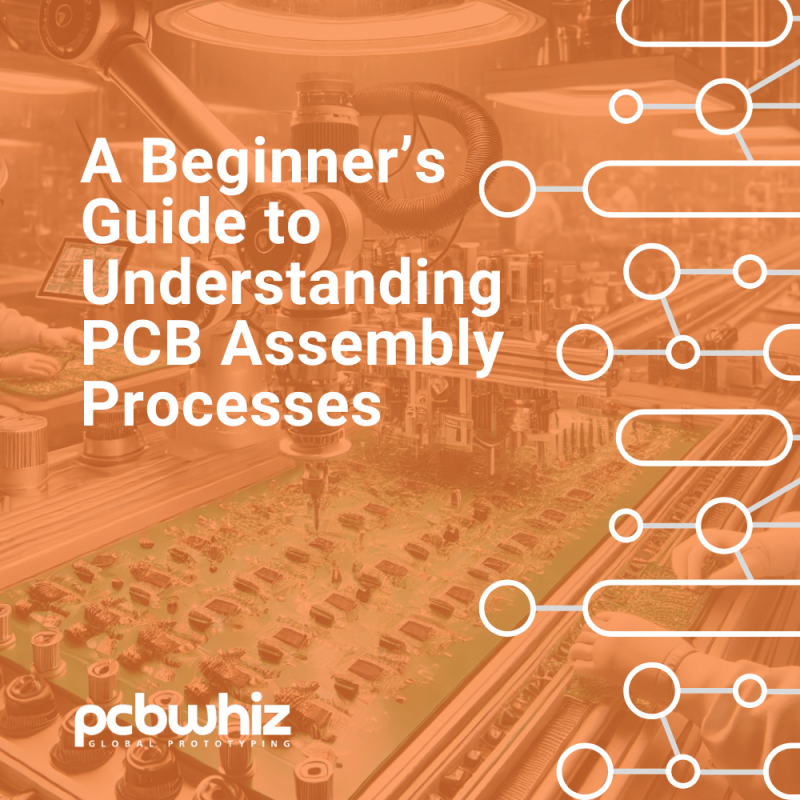
A Beginner’s Guide to Understanding PCB Assembly Processes
Die Leiterplattenbestückung (Printed Circuit Board Assembly, PCBA) ist eine entscheidende
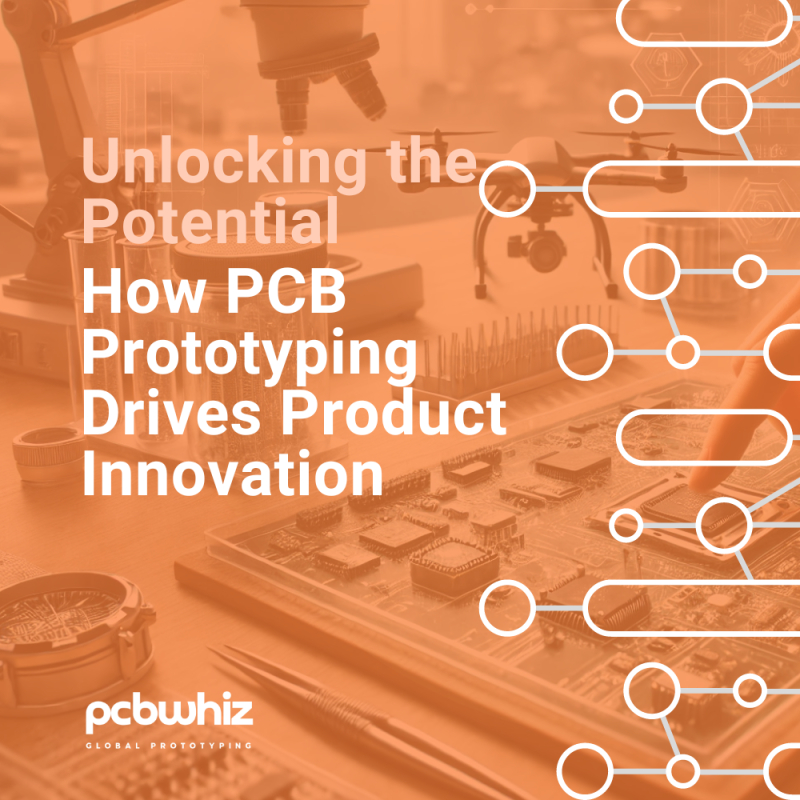
Unlocking the Potential: How PCB Prototyping Drives Product Innovation
Innovation ist der Herzschlag jeder Branche, treibt den Fortschritt voran,