Designing for Reliability - Ensuring PCB Performance in Harsh Environments
Martin Huang
Posted on January 25, 2024
In today's fast-paced and technologically advanced world, electronic devices are becoming increasingly pervasive in various industries. From automotive and aerospace applications to industrial and outdoor installations, electronic systems are often subjected to harsh and challenging environments. These environments pose unique challenges to the performance and reliability of Printed Circuit Boards (PCBs). In this article, we will delve into the critical aspects of designing for reliability and ensuring optimal PCB performance in harsh environments.
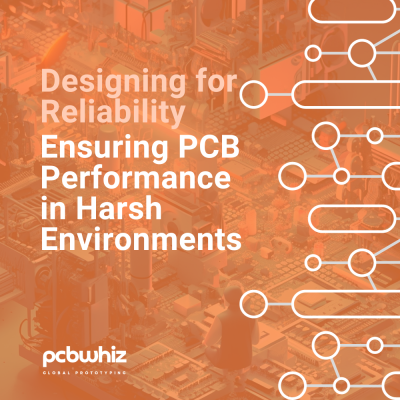
Understanding Harsh Environment Challenges
Harsh environments present a wide array of challenges for PCBs. Extreme temperatures, high humidity levels, corrosive substances, vibrations, and mechanical shocks are just a few examples of the stresses that electronic components may encounter. To ensure the longevity and reliability of PCBs in such conditions, it is crucial to understand the environmental factors that can impact their performance throughout their lifecycle.
Material Selection for Durability
The selection of appropriate materials is fundamental when designing PCBs for harsh environments. High-quality, durable materials that can withstand temperature extremes, moisture, and exposure to chemicals are essential for ensuring long-term reliability. Robust copper foils, high-temperature laminates, and conformal coatings are among the components and materials that play a significant role in protecting PCBs from environmental stressors.
Thermal Management for Temperature Extremes
Temperature variations can have a profound impact on the performance and reliability of PCBs. Proper thermal management is critical to dissipate heat effectively and maintain optimal operating temperatures. Techniques such as heat sinks, thermal vias, and efficient component placement contribute to the dissipation of heat and prevent overheating, ensuring reliable operation in harsh temperature environments.
Sealing and Encapsulation for Protection
Moisture, dust, and other contaminants can severely impact the performance of PCBs. To safeguard against these elements, sealing and encapsulation techniques are employed. Conformal coatings, potting compounds, and encapsulation materials create a protective barrier around the PCB, preventing the ingress of harmful substances. These techniques are particularly crucial for applications exposed to high humidity, water, or corrosive substances.
Vibration and Shock Resistance
In harsh environments, PCBs are often subjected to vibrations and mechanical shocks that can lead to component failure. Design considerations such as secure mounting, vibration dampening, and mechanical reinforcement are essential to mitigate the effects of these stresses. Additionally, selecting components with appropriate shock and vibration resistance ratings is vital for ensuring the long-term reliability of PCBs in challenging environments.
Electromagnetic Interference (EMI) Shielding
Harsh environments can be rife with electromagnetic interference (EMI), which can disrupt the performance of electronic systems. EMI shielding techniques are critical for reducing the impact of electromagnetic noise on PCBs. Using conductive enclosures, shielding materials, proper grounding, and signal routing techniques are effective ways to minimize EMI and maintain signal integrity in harsh environments.
Environmental Testing and Compliance
Thorough environmental testing is necessary to validate the reliability of PCB designs for harsh environments. Testing methodologies such as temperature cycling, humidity testing, accelerated aging, and shock and vibration testing simulate the conditions that PCBs may encounter during their operational lifespan. Compliance with industry standards and regulations ensures that PCBs meet specific environmental requirements and perform reliably in challenging environments.
Collaboration with PCB Manufacturers
Designing PCBs for reliability in harsh environments requires close collaboration between design engineers and PCB manufacturers. PCB manufacturers with expertise in producing ruggedized boards for harsh environments can provide valuable insights and guidance throughout the design process. Their knowledge of materials, manufacturing techniques, and testing procedures can significantly enhance the reliability and performance of PCBs in challenging conditions.
Conclusion
Designing PCBs for reliable performance in harsh environments is a critical aspect of ensuring the longevity and functionality of electronic systems in demanding industries. By carefully considering factors such as material selection, thermal management, sealing, vibration resistance, EMI shielding, and compliance with environmental standards, design engineers can create robust PCB designs. Collaboration with experienced PCB manufacturers further enhances the reliability and performance of PCBs in harsh environments.
In the ever-evolving landscape of industrial automation, where technologies push boundaries and industries demand electronics that can withstand even more challenging conditions, the importance of designing for reliability in harsh environments will only increase. By prioritizing robust design practices and collaborating with experienced partners, companies can ensure the performance and longevity of their electronic systems in the face of environmental adversity.
If you found this article informative, stay tuned for more discussions on PCB design and manufacturing best practices, as we explore the fascinating world of electronic reliability in various applications and environments.
Keep Reading...
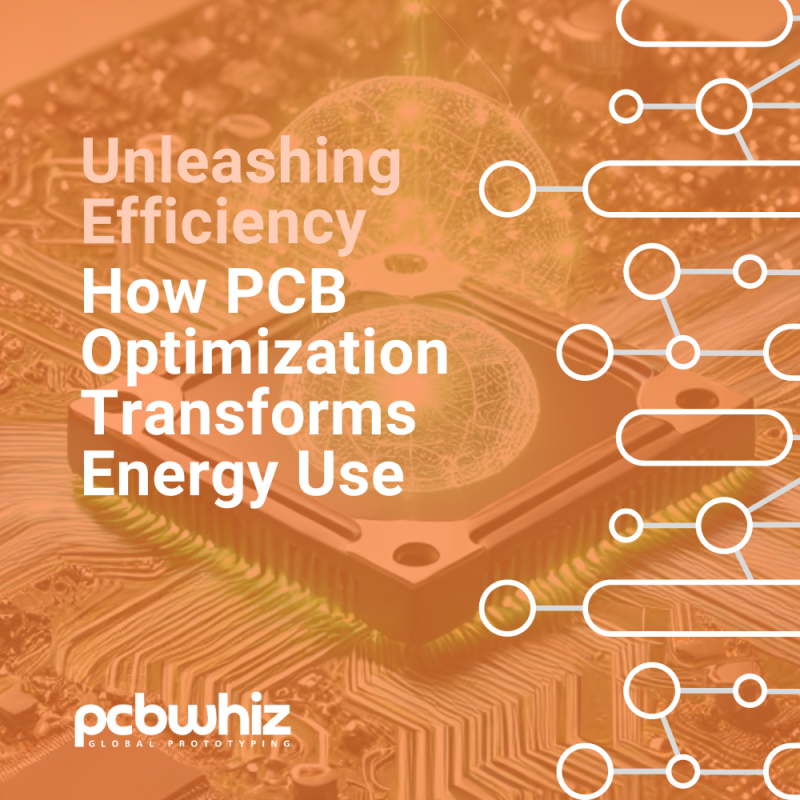
Unleashing Efficiency: How PCB Optimization Transforms Energy Use
In einer Welt, in der Energieeinsparung und Nachhaltigkeit von größter

Unleashing Creativity: How PCB Engineering Empowers Electronic Innovation
Kreativität treibt Innovationen an, und in der Welt der Elektronik
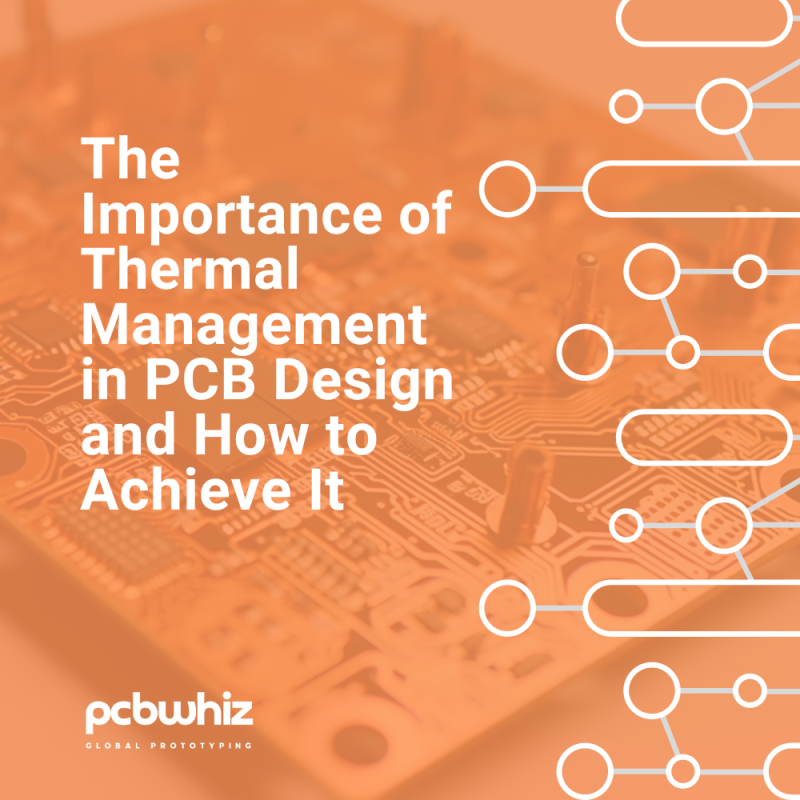
The Importance of Thermal Management in PCB Design and How to Achieve It
Das Wärmemanagement ist ein kritischer Aspekt des Leiterplattendesigns, der oft