The electronics industry is undergoing rapid and unprecedented change, thanks in large part to Industry 4.0. Industry 4.0, also known as the fourth industrial revolution, is a term used to describe the integration of digital technologies and physical systems. It encompasses a range of technologies, including artificial intelligence, the Internet of Things (IoT), cloud computing, and big data analytics. In the PCB manufacturing industry, Industry 4.0 is already having a significant impact. In this post, we'll explore the ways in which Industry 4.0 is transforming PCB manufacturing and what engineers can expect in the years to come.
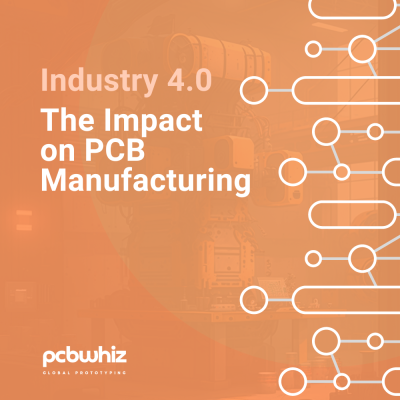
- Predictive Maintenance and Quality Control
One of the most significant benefits of Industry 4.0 technologies is predictive maintenance. Predictive maintenance is the practice of using data analytics and machine learning algorithms to predict when equipment is likely to fail. This allows manufacturers to schedule maintenance proactively, reducing downtime and increasing overall efficiency.
In the PCB manufacturing industry, predictive maintenance is particularly valuable. PCB manufacturing involves a large number of complex and expensive machines, which can be prone to failure. By using predictive maintenance, manufacturers can avoid costly repairs and replacements, ensuring that their machines are always operating at peak efficiency.
Predictive maintenance also has applications in quality control. By analyzing data from sensors and other sources, manufacturers can identify patterns and anomalies that indicate a defect in the PCB or the manufacturing process. This allows engineers to take corrective action before the defect becomes a serious problem, improving the overall quality of the PCB.
- Smart Factories
Another way in which Industry 4.0 is transforming PCB manufacturing is through the use of smart factories. Smart factories are factories that use advanced digital technologies to optimize manufacturing processes and improve efficiency. They use technologies such as IoT, machine learning, and robotics to automate tasks and optimize production.
In the PCB manufacturing industry, smart factories have numerous benefits. They can improve efficiency by reducing downtime and increasing productivity. They can also reduce costs by automating tasks that were previously done manually. This can lead to lower labor costs and a faster time to market for new PCBs.
Smart factories also have the potential to improve safety in the PCB manufacturing industry. By using robotics and automation, manufacturers can reduce the risk of accidents and injuries caused by manual labor. This can make the PCB manufacturing process safer for workers and reduce the risk of liability for manufacturers.
- Increased Customization
Another way in which Industry 4.0 is transforming PCB manufacturing is through increased customization. The PCB manufacturing process has traditionally been a highly standardized process, with little room for customization. However, with the introduction of Industry 4.0 technologies, this is changing.
Industry 4.0 technologies such as 3D printing and machine learning are enabling manufacturers to create custom PCBs more easily and quickly than ever before. By using 3D printing, manufacturers can create custom PCBs that are tailored to a specific application or device. Machine learning algorithms can help engineers to design PCBs that are optimized for specific use cases.
Increased customization has numerous benefits for the PCB manufacturing industry. It allows manufacturers to create PCBs that are better suited to specific applications, improving performance and reliability. It can also lead to a faster time to market for new PCBs, as manufacturers can quickly design and produce custom PCBs to meet the needs of their customers.
- Improved Supply Chain Management
Industry 4.0 technologies are also transforming supply chain management in the PCB manufacturing industry. By using IoT sensors and other technologies, manufacturers can track the location and status of components and raw materials in real-time. This allows them to optimize their supply chains, reducing the risk of delays and shortages.
Improved supply chain management also enables PCB manufacturers to achieve greater transparency and traceability in their operations. This is particularly important for companies that operate in heavily regulated industries such as aerospace and defense, where compliance with strict quality standards is essential. By using IoT sensors and other technologies, manufacturers can track the entire lifecycle of a product, from its raw materials to its final assembly and delivery. This not only helps ensure compliance with regulatory requirements but also enables manufacturers to quickly identify and address any quality issues that arise.
Overall, the impact of Industry 4.0 on the PCB manufacturing industry is significant and far-reaching. By embracing these technologies, manufacturers can improve their efficiency, reduce costs, and deliver higher quality products to their customers. However, realizing these benefits requires careful planning and execution. PCB manufacturers must be willing to invest in the necessary technologies and expertise to make the most of these innovations.
Smart Factories and the PCB Manufacturing Process
One of the most significant changes that Industry 4.0 is bringing to PCB manufacturing is the concept of smart factories. Smart factories are fully connected facilities that leverage technologies such as artificial intelligence, machine learning, and the IoT to optimize production processes and improve overall efficiency.
In the context of PCB manufacturing, smart factories can have a profound impact on the production process. For instance, with the help of sensors and real-time data analytics, manufacturers can monitor the entire production process from start to finish. This includes tracking the performance of equipment, monitoring the quality of raw materials, and identifying potential bottlenecks in the production process.
One of the key benefits of smart factories is that they enable manufacturers to optimize their processes in real-time. For example, if a particular machine is not performing optimally, the system can automatically identify the issue and send an alert to maintenance staff. Similarly, if a particular batch of raw material does not meet the required quality standards, the system can automatically adjust the manufacturing process to compensate for the deficiency.
Furthermore, smart factories can enable manufacturers to offer new types of services to customers. For example, by leveraging data analytics, manufacturers can offer predictive maintenance services that identify potential equipment failures before they occur. This can help customers minimize downtime and improve overall equipment efficiency.
Artificial Intelligence and Machine Learning in PCB Manufacturing
Another key aspect of Industry 4.0 that is transforming PCB manufacturing is the use of artificial intelligence and machine learning. These technologies are being used to automate a range of tasks, from design and layout to testing and quality control.
One of the most significant benefits of AI and machine learning in PCB manufacturing is their ability to automate the design process. PCB design is a complex task that involves a range of considerations, such as component placement, signal routing, and thermal management. With the help of AI and machine learning, engineers can now automate many of these tasks, freeing up valuable time for more critical design work.
Another area where AI and machine learning are making an impact is in testing and quality control. Traditionally, testing and quality control have been manual processes that involve a significant amount of human labor. However, with the help of AI and machine learning, manufacturers can now automate many of these processes, reducing the risk of errors and improving overall efficiency.
For example, machine learning algorithms can be trained to identify defects in PCBs, such as shorts and opens, with a high degree of accuracy. Similarly, AI-powered vision systems can be used to inspect PCBs for cosmetic defects, such as scratches and discoloration.
The Future of PCB Manufacturing
As we move further into the era of Industry 4.0, it's clear that the PCB manufacturing landscape will continue to evolve. The rise of smart factories, artificial intelligence, and the IoT is enabling manufacturers to produce PCBs faster, more efficiently, and with higher quality than ever before.
However, as with any significant technological change, there will be challenges that manufacturers must overcome. For example, the rise of smart factories and automation could potentially lead to job losses in certain sectors of the industry. Similarly, the complexity of Industry 4.0 technologies could pose a challenge for smaller manufacturers who may not have the resources to invest in these new technologies.
Despite these challenges, it's clear that Industry 4.0 is transforming the PCB manufacturing landscape in profound ways. By leveraging these new technologies, manufacturers can improve their efficiency, reduce costs, and offer new types of services to customers. As the industry continues to evolve, it will be exciting to see what new innovations emerge and how they will shape the future of PCB manufacturing.
Keep Reading...
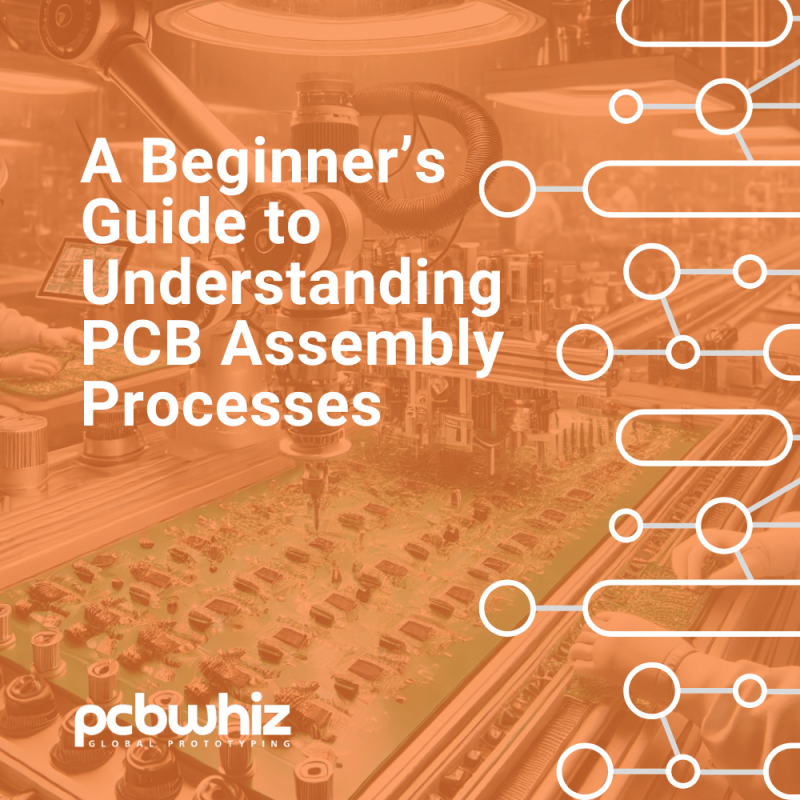
A Beginner’s Guide to Understanding PCB Assembly Processes
Die Leiterplattenbestückung (Printed Circuit Board Assembly, PCBA) ist eine entscheidende
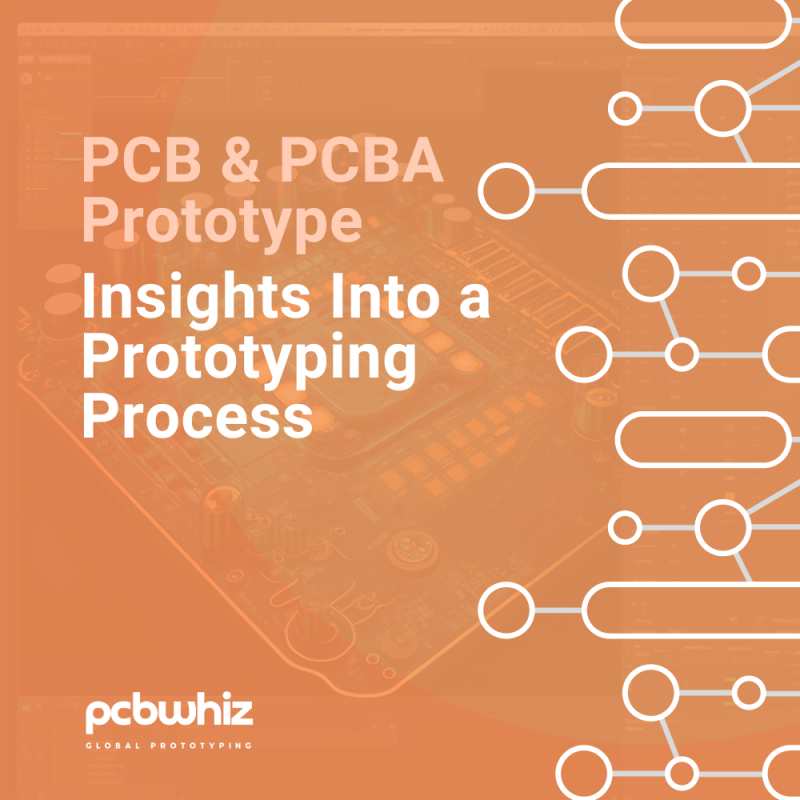
PCB & PCBA Prototype - Insights into a prototyping process
Leiterplatten (PCBs) sind wesentliche Bestandteile der modernen Elektronik und dienen