Unleashing Efficiency: How PCB Optimization Transforms Energy Use
Martin Huang
Posted on August 15, 2024
In a world where energy conservation and sustainability are paramount, enhancing energy efficiency is crucial across all industries. From smartphones to industrial machinery, electronic devices consume significant energy. Optimizing Printed Circuit Boards (PCBs) is a key strategy to enhance energy efficiency by minimizing power consumption, reducing heat dissipation, and improving overall system performance. Let's explore how PCB optimization unlocks efficiency and fosters greener, more sustainable electronic solutions.
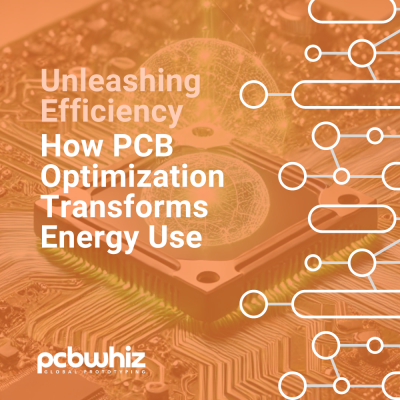
Power Distribution Optimization
Efficient power distribution is fundamental to energy-efficient electronic systems. PCB optimization focuses on minimizing power losses and ensuring precise power delivery to reduce waste and improve energy utilization. Here are some techniques:
1. Power Plane Design:
Strategic power plane design within the PCB stack-up ensures efficient power distribution. Power planes provide low-impedance pathways, reducing resistance and voltage drops. By designing these planes carefully and ensuring adequate copper pour, power losses are minimized, enhancing overall energy efficiency.
2. Power Supply Placement:
Optimal placement of power supply components, such as voltage regulators and capacitors, is essential for efficient power distribution. Positioning these components near power-hungry parts reduces trace lengths and resistance, minimizing voltage drops, ensuring stable power supply, and boosting energy efficiency.
3. Signal Integrity Considerations:
Addressing signal integrity is crucial in reducing power-related issues. Proper termination techniques, impedance control, and signal integrity analysis help prevent signal reflections, crosstalk, and electromagnetic interference (EMI). Mitigating these issues minimizes power-related noise, leading to improved energy efficiency.
Component Selection and Placement
Choosing and placing components wisely is critical for energy-efficient PCB optimization. Engineers select components based on power requirements, efficiency ratings, and thermal characteristics. Key considerations include:
1. Low Power Components:
Selecting components with low power consumption and high efficiency is vital for energy-efficient PCB design. Using power-efficient microcontrollers, low-power integrated circuits, and energy-saving sensors significantly reduces overall power consumption.
2. Thermal Considerations:
Heat dissipation is a significant factor in energy efficiency. Overheating can reduce component lifespan, degrade performance, and even cause system failure. Strategic component placement facilitates efficient heat dissipation. Placing heat-generating components near heat sinks, thermal vias, and copper pours enhances heat dissipation and overall energy efficiency.
3. Power Management ICs:
Integrating advanced power management ICs enhances energy efficiency. These ICs enable efficient power conversion, voltage regulation, and power sequencing. By dynamically adjusting power supply levels based on system requirements, power management ICs minimize power wastage and enhance energy efficiency.
Signal Routing and Trace Optimization
Efficient signal routing and trace optimization are vital for energy-efficient PCB design. Well-designed signal paths and optimized trace layouts reduce signal degradation, minimize crosstalk, and enhance signal integrity, resulting in lower power losses and improved energy efficiency. Considerations include:
1. Trace Length and Width:
Optimizing trace length and width minimizes resistance, capacitance, and inductance. Shorter traces reduce signal propagation delays, while wider traces lower resistance, minimizing power losses. Careful calculation of trace widths and lengths based on current-carrying capacity and impedance requirements maximizes energy efficiency.
2. Ground and Power Plane Placement:
Effective ground and power plane placement reduces noise and enhances signal integrity. Properly positioned ground planes provide shielding, minimize signal interference, and improve noise immunity. Optimizing the placement of ground and power planes maintains signal quality and improves energy efficiency.
3. High-Speed Design Considerations:
In high-speed PCB designs, signal integrity is critical. PCB optimization involves impedance matching, controlled impedance routing, and advanced signal integrity techniques. Minimizing signal reflections, ensuring clean signal transitions, and reducing noise enhances energy efficiency in high-speed electronic systems.
Thermal Management Techniques
Efficient thermal management is essential for energy-efficient PCB optimization. Excessive heat affects component performance and reliability, leading to energy wastage and decreased system efficiency. Various thermal management techniques enhance energy efficiency:
1. Heat Sink Design:
Strategic placement of heat sinks on heat-generating components facilitates efficient heat dissipation. Optimized heat sink designs and materials transfer heat away from critical components, improving energy efficiency.
2. Thermal Vias and Copper Pours:
Thermal vias and copper pours enhance heat dissipation by providing additional thermal pathways. Strategic placement of thermal vias in heat-intensive areas allows heat to flow efficiently through PCB layers. Copper pours spread heat across larger areas, preventing localized heating and improving overall energy efficiency.
3. Simulation and Analysis:
Thermal simulation and analysis tools predict and mitigate thermal issues. Simulating heat dissipation, temperature distribution, and airflow patterns helps identify potential hotspots and optimize the PCB layout. This proactive approach ensures effective thermal management, minimizing energy wastage due to excessive heat.
Testing and Validation
Thorough testing and validation are integral to PCB optimization for energy efficiency. Rigorous testing ensures the optimized PCB design meets desired energy efficiency goals. Key testing methodologies include:
1. Power Consumption Analysis:
Measuring and analyzing power consumption under different operating conditions identifies power-hungry components, areas of power wastage, and opportunities for further optimization. Continuous measurement and fine-tuning of power consumption improve energy efficiency.
2. Thermal Analysis:
Comprehensive thermal analysis evaluates the effectiveness of thermal management techniques. Thermal imaging, thermal conductivity analysis, and temperature measurements identify thermal inefficiencies. Validating the thermal performance of the PCB design optimizes energy efficiency and mitigates potential thermal issues.
3. Performance Evaluation:
Evaluating overall system performance ensures that energy efficiency enhancements do not compromise functionality or reliability. Performance tests assess the system's ability to deliver desired functionality within defined energy efficiency parameters. Balancing energy efficiency with performance requirements achieves the desired balance between power savings and functionality.
Conclusion
PCB optimization is pivotal in enhancing energy efficiency and driving greener, more sustainable electronic solutions. By focusing on power distribution optimization, component selection and placement, signal routing and trace optimization, thermal management techniques, and rigorous testing and validation, PCB engineers unleash the full potential of energy efficiency. Energy-efficient PCB designs reduce power consumption, minimize heat dissipation, and improve system performance.
In a world striving for energy conservation and sustainability, optimizing PCB designs for energy efficiency is not only a competitive advantage but also a responsibility. By embracing PCB optimization principles, companies contribute to a greener future while achieving cost savings and improved system performance.
Stay tuned for more insights on PCB optimization, energy-efficient design techniques, and emerging technologies shaping the future of energy-conscious electronic systems.
Keep Reading...
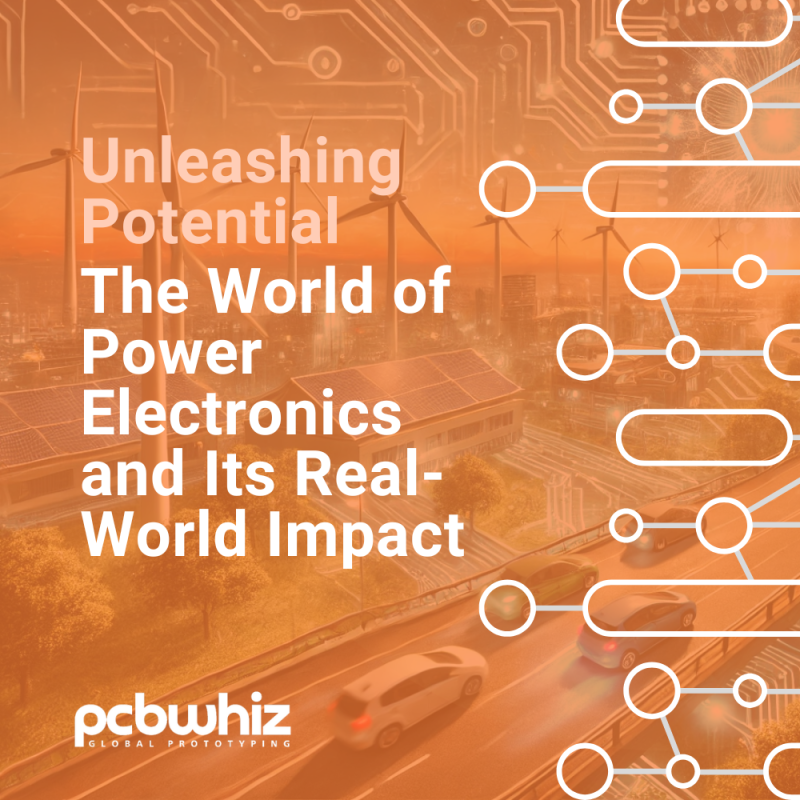
Unleashing Potential: The World of Power Electronics and Its Real-World Impact
Leistungselektronik mag nicht die glamouröseste Disziplin der Ingenieurwissenschaften sein, doch
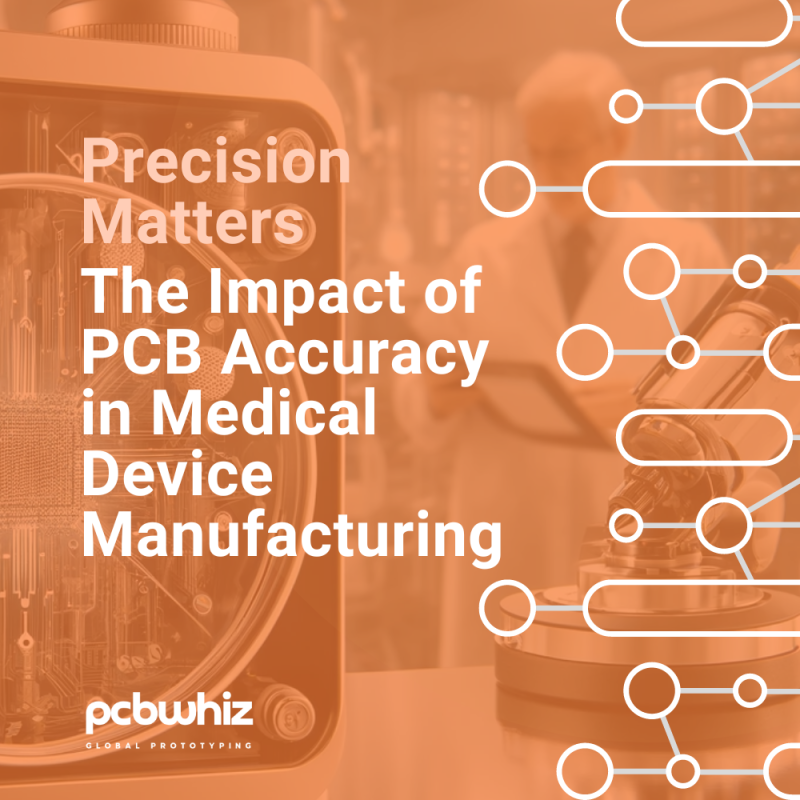
The Impact of PCB Accuracy in Medical Device Manufacturing
Im Bereich der Herstellung medizinischer Geräte sind Präzision und Genauigkeit
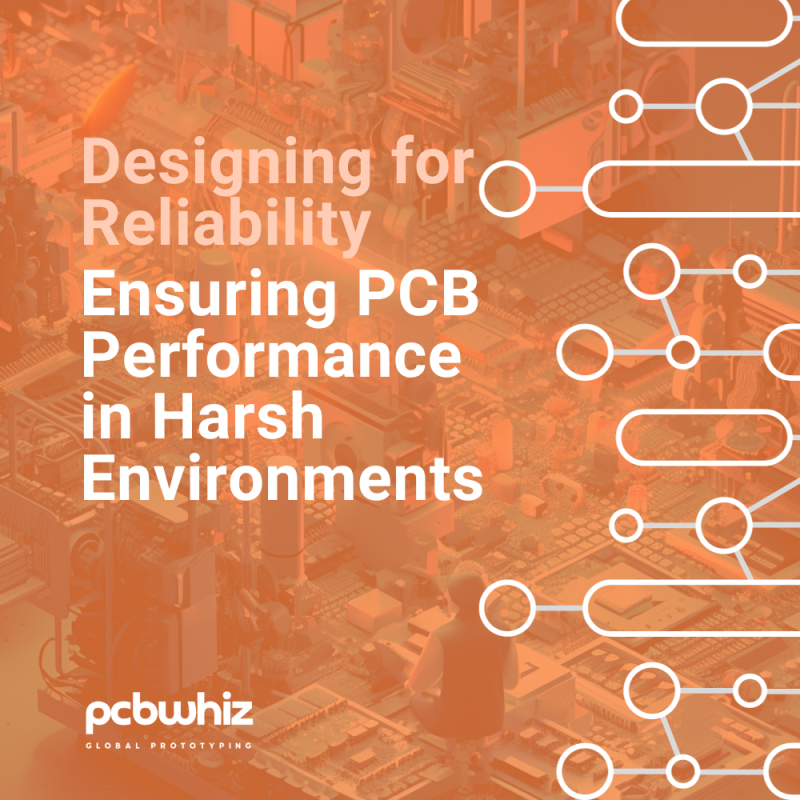
Designing for Reliability - Ensuring PCB Performance in Harsh Environments
In der schnelllebigen und technologisch fortschrittlichen Welt von heute sind